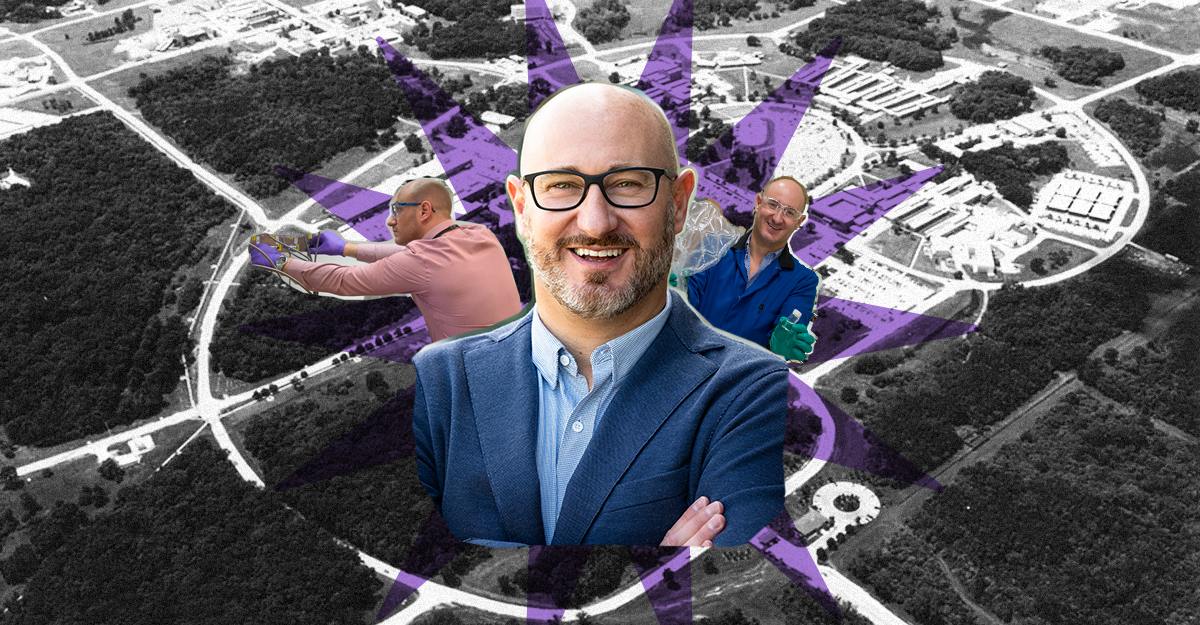
Dr. Max Delferro, Argonne National Lab, Building a World With Sustainable Plastics
The U.S. Department of Energy’s (DOE) Office of Technology Transfers is holding a series of webinars on cutting-edge technologies being developed at the DOE National Labs – and the transformative applications they could have globally for clean energy. We sat down with the people behind these technologies – the experts who make that progress possible. These interviews highlight why a strong energy workforce is so important, from the lab into commercial markets. These interviews have been edited for length and do not necessarily reflect the views of the DOE. Be sure to attend DOE’s next National Lab Discovery Series webinar on catalysts for plastics upcycling on Thursday, August 22.
Dr. Max Delferro has spent his career bringing research on plastics recycling to the forefront of scientific discussions. Since 2008, he has focused on how to effectively and economically recycle plastics – but also how to turn them into more valuable materials like synthetic oils and waxes. As a Group Leader of the Catalysis Science Program Group at Argonne National Laboratory, Dr. Delferro’s work could help take plastic out of landfills and put them to good use elsewhere.
A Post-doctorate in Plastics Manufacturing
After completing three degrees – including a PhD – at the University of Parma in Italy, Dr. Delferro moved to Chicago, where he took up a postdoc position at Northwestern University. With a background in organometallic chemistry, Dr. Delferro hadn’t considered working on polymer synthesis until he started his postdoc.
“When I first came to Northwestern after my PhD, they were working on the development of new catalysts to make polymers, such as polyethylene,” Dr. Delferro said. “I had zero knowledge of how to do this at first, but I initiated my first ethylene polymerization – it took a few seconds – and a white powder started to precipitate. It was amazing.”
That was 16 years ago – a time when plastics accumulation in the environment wasn’t yet a hot topic for public discussion like it is today. Now, as Dr. Delferro says, there is at least one article in every journal or newspaper at any given time discussing the role and impact of plastics in our society.
“It took circa 100 years of research on how to make efficient and functional polymers. We’ve created a polymer that can go into space, and we’ve produced a polymer that uses the same material but has completely different properties to make a plastic bag. Scientists have mastered the engineering and design of how to make these polymers, but we still don’t know how to efficiently deconstruct them.”
After he joined Argonne National Laboratory in 2016, Dr. Delferrro started to think on how to convert plastics into new products. However, the first feedback he received was why anyone should care about plastics deconstruction when there’s plenty of landfills to dispose of plastics.
“Maybe in 20, 30, 50 years there will be no more room in landfills,” Dr. Delferro responded. “What are we going to do with that material then? We will need to discover how to selectively deconstruct plastics, in particular polyolefins.”
Polyolefins are a class of polymers that make up about 50 to 64% of the world’s plastic waste. They are not biodegradable, causing them to accumulate in landfills or wherever they’re disposed of.
Over dinner, Dr. Delferro and his colleagues discussed this idea and how to apply for funding to research this exact question. A white paper was sent to DOE’s Office of Science, Basic Energy Science which initially funded the project, followed by funding through the Energy Frontier Research Center, Institute for Cooperative Upcycling of Plastics (ICOUP). Dr. Delferro’s research could begin.
Uncovering the Problem of Plastics Recycling
Everything started when Dr. Delferro and his colleagues paid a visit to a nearby recycling facility to take a peek “behind the scenes.” Unbeknownst to him, what he would see that day would alter his research trajectory.
“It’s really not efficient how we do recycling in the United States. All of the plastics move along on a very, very fast conveyor belt. To separate a plastic bottle from the rest, there are detectors that recognize the bottles and then activate an air jet that pushes the bottle off of the belt. But if you have any light plastics, like a plastic bag, the bag also flies away with the bottle. Then, the recyclable bottles, made of polyethylene terephthalate (PET, #1), became contaminated with an unrecyclable plastic bag, which makes the PET items unrecyclable.”
It was at this moment that Dr. Delferro first decided to focus his attention on the problem of plastics recycling.
“It was because of this experience that I thought, ‘Okay, we need to do something.’ Which is when we started to focus on plastics. Seeing with my own eyes was a game changer. I could not believe how we are managing plastic waste right now.”
In Dr. Delferro’s native Italy, for example, the recycling system is more robust.
“When I visit my mom in the summer, she has seven different bins – one yellow, another blue, a green, a brown, etc, and the city gives her a bag with an RFID tag that they scan. And if they open it and they find, for example, unwashed glass or plastic in the metal bin, she gets a fine.”
Without a system like this in place, the U.S. relies on individuals who recycle to know how to do it properly. During Argonne Open Lab Day, Dr. Delferro informed the public about what all goes into recycling, but is sometimes met with confusion.
“I think 95% of the people who come to our open labs don’t understand how to recycle correctly. On every piece of plastic, there is a symbol with a number from one to seven. To date, only numbers one and two should go into the blue bin. For three to seven, we need to develop new technologies and new processes to target [those plastics] – which is what we’re doing at the DOE National lab system.”
Dr. Delferro’s lab especially focuses on plastics that fall in categories four and five. Number four plastics are known as LDPEs, like the kind used in grocery bags and shrink wrap. Number five – polypropylene – are used for items like yogurt cups, bottle caps, and ketchup bottles. Consider a plastic soda bottle, for instance, that uses both kinds of plastic – a sturdy twist-off cap made from polypropylene and a wraparound brand label that uses a stretchier LDPE.
“In theory, the PET bottle is 100% recyclable and can be recycled an infinite number of times without losing its mechanical and thermal properties. For the polypropylene cap, a few new technologies are just now coming out on the market. Up until a few years ago, this cap would end up in a landfill.”
While the LDPE used to make the brand label plastic film now costs less than a penny to manufacture, the research and development required to design a material with its specific properties took decades. Now, Dr. Delferro and his team are faced with the challenge of discovering a technology to selectively deconstruct LDPE and other kinds of polyolefins like it.
“One technology doesn’t solve all of the problems that we have. We probably need one hundred technologies to solve all of these problems, and we are only at the beginning phases of the inception of each of these.”
One Man’s Trash is another Man’s Synthetic Oil
Working at Argonne, Dr. Delferro gets the opportunity to explore these solutions – and has developed a catalyst technology that could help not only recycle, but upcycle plastic into more valuable items.
“I pay taxes for the city to come pick up my trash, but what if, instead, we had an economy where trash became valuable? Then I could leave my plastic jug and someone would be incentivized to pick it up for money. If we were to value plastic bottles at, say, one cent per bottle, it would make a big difference. How many bottles are in one blue bin? How many blue bins per alley? How many alleys per street? My job is to develop the technologies to incentivize this process.”
Dr. Delferro is confident that developing these technologies is not a matter of if, but when.
“From a technological and scientific point of view, we are going to solve the plastic deconstruction problem. I don’t know when, but we, as a science community, are going to develop the technologies to solve it. The most difficult part is really the economics.”
While the economics may be the “most difficult part” to understand in Dr. Delferro’s brain, the polymer science itself is no walk in the park. The most current type of selective deconstruction is called pyrolysis. This process begins with plastic waste that is burned, without oxygen, to produce a mixture of gas, liquids, and solid products. The liquid oils, after separation, can be blended with crude oil to be sent back to a refinery to remake new olefins (like propane, ethene, or butene).
“Pyrolysis is great, but we think that there are more opportunities that exist outside of it. It’s not very selective, it creates a lot of byproducts that require separation, there are gasses involved, and so on.”
So, Dr. Delferro and his team began exploring hydrogenolysis – a very selective way of combining hydrogen in presence of a catalyst to selectively chop polymeric chains, through carbon-carbon cleavage. What they found was that they were able to fine tune the property of the newly-discovered catalysts to make a selective product – like waxes and lubricants – without the requirement of any separation.
“Our dream is for you to be able to go into the car mechanic, or wherever you change the oil in your car, and they can change the oil in your car with synthetic oil that comes directly from plastic waste. That is our dream and our vision.”
The Argonne scientists aren’t the only believers in this vision of converting waste into a resource. The Bioenergy Technologies Office (BETO) and Advanced Materials & Manufacturing Technologies Office (AMMTO) at the DOE, in collaboration with Chevron Phillips – one of the biggest producers of lubricating based-oil – are supporting this project.
“Maybe one day, your plastic bag could become the oil for your car. And that is our goal.”
The Power of Lab Science
Max’s work is only possible because of the institution supporting him. His support comes from “all over the place” within DOE offices. His core program is primarily supported by the DOE Office of Basic Energy Sciences, in particular the Chemical Sciences, Geosciences, and Biosciences Division (CSGB).
Dr. Delferro is involved with two Energy Frontier Research Centers (EFRC) – basic research programs funded by DOE. He is the Deputy Director of the Institute for Cooperative Upcycling of Plastics, led by Ames Lab, and a principal investigator at the Catalyst Design for Decarbonization Center (CD4DC) at the University of Chicago that is working on hydrogen management.
“At UChicago, we are using metal organic frameworks – porous materials that we designed to do hydrogen management. These materials add or remove hydrogen to molecules to transport the molecules from point A to point B, which will be very, very important in the future for the hydrogen economy.”
When it comes to the plastic conversion conversation, Argonne and Ames National Laboratories are leading the basic science research efforts, joined by the BOTTLE Consortium – led by the National Renewable Energy Laboratory (NREL) and composed of experts from other labs and universities – on the applied science side.
“There are a lot of people that are working in this conversion area and the National Labs play a pivotal role. [Argonne and Ames Labs] just had our first joint meeting [with the BOTTLE Consortium] in May of this year to have an open conversation and see what we are each doing and how we can work together to push for new technology and knowledge.”
The National Labs are more about us than about me.
And it’s not just funding that makes a difference. Max’s position at Argonne means collaboration is often just a few doors down.
“In my research group, I have a physicist, a computational engineer … Everyone can bring their expertise to the table to tackle really difficult projects that one person could not do alone. When I want to learn about quantum computing, I go down one set of stairs where there’s a quantum computer. The National Labs are more about us than about me.”
It doesn’t stop there – Max’s research is able to be licensed by private companies.
“We have a series of patents as they go from catalyst design process and applications. They are available for everyone to be licensed,” Dr. Delferro said. “Two of my postdocs that left when they finished their postdoc here got some of this IP and they started their own startup company called Aeternal Upcycling, with ideas to try to take this technology from the lab to the market.”
Putting the Impact in Plastic
The beauty of working at an institution like Argonne National Lab is that researchers like Dr. Delferro can join forces with scientists in other fields to tackle complex problems. Dr. Delferro brought his expertise in catalyst design to the Manufacturing Group and the Life Cycle Analysis Group at Argonne, whose researchers stepped in to fill gaps in his own knowledge.
After conducting rounds of research, this team of researchers found that making oil from plastic waste produces 50% less carbon emissions than the oil from the refinery.
“Right then you start to think, ‘Oh maybe this could have an impact.’”
Dr. Delferro sees the importance of his work not only in the lab, but out in the world, too.
“When you go on a beautiful beach, when you see a straw, you say, ‘Dang it, why use a straw? Why do you need a straw? You don’t need a straw. Why is there a straw here? My beautiful beach, can I do something?’”
An example like this illustrates that while Dr. Delferro is working to deconstruct polyethylenes in his lab, his friends and neighbors are also interacting closely with these same materials in their own lives.
“The beauty of this research compared with other research is if I talk with my neighbor about quantum computing, they don’t have a clue about the physics behind it. If I talk about plastic waste and how we should do recycling, everyone can understand.”
Dr. Pierre-Clément Simon and Dr. Casey Icenhour come from different backgrounds, but share similar passions: for driving forward progress in fusion energy and mentoring early career scientists.
Dr. Onar’s work today will enable faster, more secure wireless charging for electric vehicle fleets, household appliances, and more.