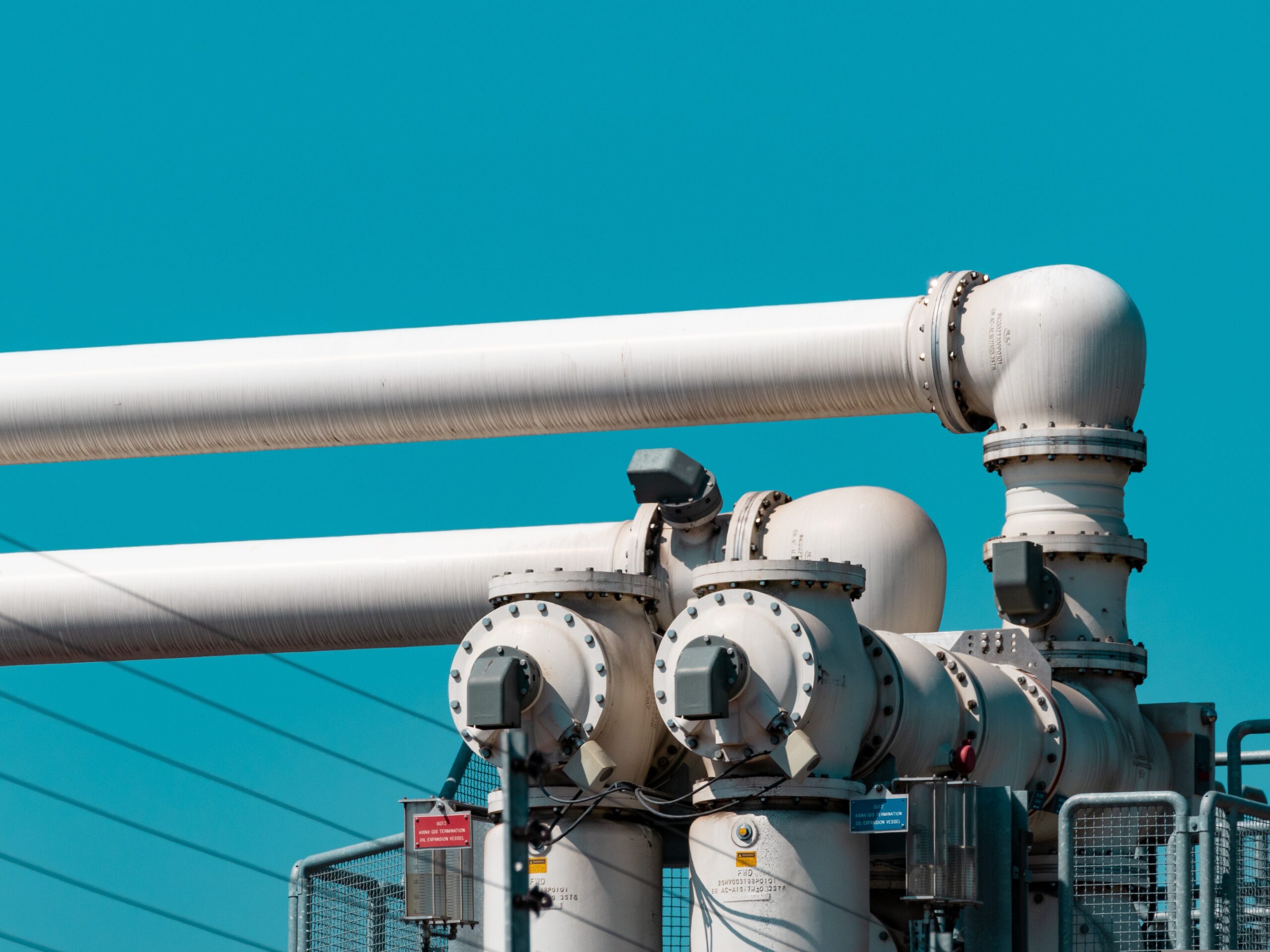
Building a National Network of Composite Pipes to Reduce Greenhouse Gas Emissions
Summary
65,000 miles of pipeline: that’s the distance that may be necessary to achieve economy-wide net-zero emissions by 2050, according to a Princeton University study. The United States is on the verge of constructing a vast network of pipelines to transport hydrogen and carbon dioxide, incentivized by the Infrastructure Investment and Jobs Act and the Inflation Reduction Act. Yet the lifecycle emissions generated by a typical steel pipeline is 27.35 kg carbon dioxide eq per ft1. Which means 65,000 miles would result in nearly 9.4 million megatons of carbon dioxide eq (equal to over 2 million passenger cars annually) produced just from steel pipeline infrastructure alone.
Pipelines made from composite materials offer one pathway to lowering emissions. Composite pipe is composed of multiple layers of different materials—typically a thermoplastic polymer as the primary structural layer with reinforcing materials such as fibers or particulate fillers to increase strength and stiffness. Some types have lifecycle emissions that are nearly one-third less than typical steel pipeline. Depending on the application, composite pipelines can be safer and less expensive. However, the process under Pipeline and Hazardous Materials and Safety Administration (PHMSA) to issue permits for composite pipe takes longer than steel, and for hydrogen and supercritical carbon dioxide, the industry lacks regulatory standards altogether. Reauthorization of the Protecting Our Infrastructure of Pipelines and Enhancing Safety (PIPES) Act offers an excellent opportunity to review the policies concerning new, less emissive pipeline technologies.
Challenge and Opportunity
Challenge
The United States is on the verge of a clean energy construction boom, expanding far beyond wind and solar energy to include infrastructure that utilizes hydrogen and carbon capture. The pump has been primed with $21 billion for demonstration projects or “hubs” in the Infrastructure Investment and Jobs Act and reinforced with another $7 billion for demonstration projects and at least $369 billion in tax credits in the Inflation Reduction Act. Congress recognized that pipelines are a critical component and provided $2.1 billion in loans and grants under the Carbon Dioxide Transportation Infrastructure Finance and Innovation Act (CIFIA).
The United States is crisscrossed by pipelines. Approximately 3.3 million miles of predominately steel pipelines convey trillions of cubic feet of natural gas and hundreds of billions of tons of liquid petroleum products each year. A far fewer 5,000 miles are used to transport carbon dioxide and only 1,600 miles are dedicated to hydrogen. Research suggests the existing pipeline network is nowhere near what is needed. According to Net Zero America, approximately 65,000 miles of pipeline will be needed to transport captured carbon dioxide to achieve economy-wide net zero emissions in the United States by 2050. The study also identifies a need for several thousand miles of pipelines to transport hydrogen within each region.
Making pipes out of steel is a carbon-intensive process, and steel manufacturing in general accounts for seven to nine percent of global greenhouse gas emissions. There are ongoing efforts to lower emissions generated from steel (i.e., “green steel”) by being more energy efficient, capturing and storing emitted carbon dioxide, recycling scrap steel combined with renewable energy, and using low-emissions hydrogen. However, cost is a significant challenge with many of these mitigation strategies. The estimated cost of transitioning global steel assets to net-zero compatible technologies by 2050 is $200 billion, in addition to a baseline average of $31 billion annually to simply meet growing demand.
Opportunity
Given the vast network of pipelines required to achieve a net-zero future, expanding use of composite pipe provides a significant opportunity for the United States to lower carbon emissions. Composite materials are highly resistant to corrosion, weigh less and are more flexible, and have improved flow capacity. This means that pipelines made from composite materials have a longer service life and require less maintenance than steel pipelines. Composite pipe can be four times faster to install, require one-third the labor to install, and have significantly lower operating costs.2 The use of composite pipe is expected to continue to grow as technological advancements make these materials more reliable and cost-effective.
Use of composite pipe is also expanding as industry seeks to improve its sustainability. We performed a lifecycle analysis on thermoplastic pipe, which is made by a process called extrusion that involves melting a thermoplastic material, such as high-density polyethylene or polyvinyl chloride, and then forcing it through a die to create a continuous tube. The tube can then be cut to the desired length and fittings can be attached to the ends to create a complete pipeline. We found that the lifecycle emissions from thermoplastic pipe were 6.83 kg carbon dioxide eq/ft and approximately 75% lower than an equivalent length of steel pipe, which has lifecycle emissions of 27.35 kg carbon dioxide eq/ft.
These estimates do not include potential differences in leaks. Specifically, composite pipe has a continuous structure that allows for the production of longer pipe sections, resulting in fewer joints and welds. In contrast, metallic pipes are often manufactured in shorter sections due to limitations in the manufacturing process. This means that more joints and welds are required to connect the sections together, which can increase the risk of leaks or other issues. Further, approximately half of the steel pipelines in the United States are over 50 years old, increasing the potential for leaks and maintenance cost.3 Another advantage of composite pipe is that it can be pulled through steel pipelines, thereby repurposing aging steel pipelines to transport different materials while also reducing the need for new rights of way and associated permits.
Despite the advantages of using composite materials, the standards have not yet been developed to allow for safe permitting to transport supercritical carbon dioxide4 and hydrogen. At the federal level, pipeline safety is administered by the Department of Transportation’s Pipeline and Hazardous Materials Administration (PHMSA).5 To ensure safe transportation of energy and other hazardous materials, PHMSA establishes national policy, sets and enforces standards, educates, and conducts research to prevent incidents. There are regulatory standards to transport supercritical carbon dioxide in steel pipe.6 However, there are no standards for composite pipe to transport either hydrogen or carbon dioxide in either a supercritical liquid, gas, or subcritical liquid state.
Repurposing existing infrastructure is critical because the siting of pipelines, regardless of type, is often challenging. Whereas natural gas pipelines and some oil pipelines can invoke eminent domain provisions under federal law such as the Natural Gas Act or Interstate Commerce Act, no such federal authorities exist for hydrogen and carbon dioxide pipelines. In some states, specific statutes address eminent domain for carbon dioxide pipelines. These laws typically establish the procedures for initiating eminent domain proceedings, determining the amount of compensation to be paid to property owners, and resolving disputes related to eminent domain. However, current efforts are under way in states such as Iowa to restrict use of state authorities to grant eminent domain to pending carbon dioxide pipelines. The challenges with eminent domain underscore the opportunity provided by technologies that allow for the repurposing of existing pipeline to transport carbon dioxide and hydrogen.
Plan of Action
How can we build a vast network of carbon dioxide and hydrogen pipelines while also using lower emissive materials?
Recommendation 1. Develop safety standards to transport hydrogen and supercritical carbon dioxide using composite pipe.
PHMSA, industry, and interested stakeholders should work together to develop safety standards to transport hydrogen and supercritical carbon dioxide using composite pipe. Without standards, there is no pathway to permit use of composite pipe. This collaboration could occur within the context of PHMSA’s recent announcement to update its standards for transporting carbon dioxide, which is being done in response to an incident in 2020 in Sartartia, MS.
Ideally, the permits could be issued using PHMSA’s normal process rather than as special permits (e.g., 49 CFR § 195.8). It takes several years to develop standards, so it is critical to launch the standard-setting process so that composite pipe can be used in Department of Energy-funded hydrogen hubs and carbon capture demonstration projects.
Europe is ahead of the United States in this regard, as the classification company DNV is currently undertaking a joint industry project to review the cost and risk of using thermoplastic pipe to transport hydrogen. This work will inform regulators in the European Union, who are currently revising standards for hydrogen infrastructure. The European Clean Hydrogen Alliance recently adopted a “Roadmap on Hydrogen Standardization” that expressly recommends setting standards for non-metallic pipes. To the extent practicable, it would benefit export markets for U.S. products if the standards were similar.
Recommendation 2. Streamline the permitting process to retrofit steel pipelines.
Congress should streamline the retrofitting of steel pipes by enacting a legislative categorical exclusion under the National Environmental Policy Act (NEPA). NEPA requires federal agencies to evaluate actions that may have a significant effect on the environment. Categorical exclusions (CEs) are categories of actions that have been determined to have no significant environmental impact and therefore do not require an environmental assessment (EA) or an environmental impact statement (EIS) before they can proceed. CEs can be processed within a few days, thereby expediting the review of eligible actions.
The CE process allows federal agencies to avoid the time and expense of preparing an EA or EIS for actions that are unlikely to have significant environmental effects. CEs are often established through agency rulemaking but can also be created by Congress as a “legislative CE.” Examples include minor construction activities, routine maintenance and repair activities, land transfers, and research and data collection. However, even if an action falls within a CE category, the agency must still conduct a review to ensure that there are no extraordinary circumstances that would warrant further analysis.
Given the urgency to deploy clean technology infrastructure, Congress should authorize federal agencies to apply a categorical exclusion where steel pipe is retrofitted using composite pipe. In such situations, the project is using an existing pipeline right-of-way, and there should be few, if any, additional environmental impacts. Should there be any extraordinary circumstances, such as substantial changes in the risk of environmental effects, federal agencies would be able to evaluate the project under an EA or EIS. A CE does not obviate the review of safety standards and other applicable, substantive laws, but simply right-sizes the procedural analysis under NEPA.
Recommendation 3. Explore opportunities to improve the policy framework for composite pipe during reauthorization of the PIPES Act.
Both of the aforementioned ideas should be considered as Congress initiates its reauthorization of the Protecting Our Infrastructure of Pipelines and Enhancing Safety (PIPES) Act of 2020. Among other improvements to pipeline safety, the PIPES Act reauthorized PHMSA through FY2023. As Congress begins work on its next reauthorization bill for PHMSA, it is the perfect time to review the state of the industry, including the potential for composite pipe to accelerate the energy transition.
Recommendation 4. Consider the embedded emissions of construction materials when funding demonstration projects.
The Office of Clean Energy Demonstrations should consider the embedded emissions of construction materials when evaluating projects for funding. Applicants that have a plan to consider embedded emissions of construction materials could receive additional weight in the selection process.
Recommendation 5. Support research and development of composite materials.
Composite materials offer advantages in many other applications, not just pipelines. The Office of Energy Efficiency and Renewable Energy (EERE) should support research to further enhance the properties of composite pipe while improving lifecycle emissions. In addition to ongoing efforts to lower the emissions intensity of steel and concrete, EERE should support innovation in alternative, composite materials for pipelines and other applications.
Conclusion
Recent legislation will spark construction of the next generation in clean energy infrastructure, and the funding also creates an opportunity to deploy construction materials with lower lifecycle emissions of greenhouse gases. This is important, because constructing vast networks of pipelines using high-emissive processes undercuts the goals of the legislation. However, the regulatory code remains an impediment by failing to provide a pathway for using composite materials. PHMSA and industry should commence discussions to create the requisite safety standards, and Congress should work with both industry and regulators to streamline the NEPA process when retrofitting steel pipelines. As America commences construction of hydrogen and carbon capture, utilization, and storage networks, reauthorization of the PIPES Act provides an excellent opportunity to significantly lower the emissions.
We compared two types of pipes: 4” API 5L X42 metallic pipe vs. 4” Baker Hughes non-metallic next generation thermoplastic flexible pipe. The analysis was conducted using FastLCA, a proprietary web application developed by Baker Hughes and certified by an independent reviewer to quantify carbon emissions from our products and services. The emission factors for the various materials and processes are based on the ecoinvent 3.5 database for global averages.
- The data for flexible pipe production is from 2020 production year and represents transport, machine, and energy usage at the Baker Hughes’ manufacturing plant located in Houston, TX.
- All raw material and energy inputs for flex pipes are taken directly from engineering and plant manufacturing data, as verified by engineering and manufacturing personnel, and represent actual usage to manufacture the flexible pipes.
- All of the data for metallic pipe production is from API 5L X42 schedule 80 pipe specifications and represent transport from Alabama and energy usage for production from global averages.
- All raw material and energy inputs for hot rolling steel are computed from ecoinvent 3.5 database emission factors. All relevant production steps and processes are modeled.
- All secondary processes are from the ecoinvent 3 database (version 3.5 compiled as of November 2018) as applied in SimaPro 9.0.0.30.
- Results are calculated using IPCC 2013 GWP 100a (IPCC AR5).
Similar to steel pipe, transporting hydrogen and carbon dioxide using composite pipe poses certain safety risks that must be carefully managed and mitigated:
- Hydrogen gas can diffuse into the composite material and cause embrittlement, which can lead to cracking and failure of the pipe.
- The composite material used in the pipe must be compatible with hydrogen and carbon dioxide. Incompatibility can cause degradation of the pipe due to permeation, leading to leaks or ruptures.
- Both hydrogen and carbon dioxide are typically transported at high pressure, which can increase the risk of pipe failure due to stress or fatigue.
- Carbon dioxide can be corrosive to certain metals, which can lead to corrosion of the pipe and eventual failure.
- Hydrogen is highly flammable and can ignite in the presence of an ignition source, such as a spark or heat.
To mitigate these safety risks, appropriate testing, inspection, and maintenance procedures must be put in place. Additionally, proper handling and transportation protocols should be followed, including strict adherence to pressure and temperature limits and precautions to prevent ignition sources. Finally, emergency response plans should be developed and implemented to address any incidents that may occur during transportation.
API Specification 15S, Spoolable Reinforced Plastic Line Pipe, covers the use of flexible composite pipe in onshore applications. The standard does not address transport of carbon dioxide and has not been incorporated into PHMSA’s regulations.
API Specification 17J, Specification for Unbonded Flexible Pipe, covers the use of flexible composite pipe in offshore applications. Similar to 15S, it does not address transport of carbon dioxide and has not been incorporated into PHMSA’s regulations.
HDPE pipe, commonly used in applications such as water supply, drainage systems, gas pipelines, and industrial processes, has similar advantages to composite pipe in terms of flexibility, ease of installation, and low maintenance requirements. It can be assembled to create seamless joints, reducing the risk of leaks. It can also be used to retrofit steel pipes as a liner per API SPEC 15LE.
HDPE pipe has been approved by PHMSA to transport natural gas under 49 CFR Part 192. However, the typical operating pressures (e.g., 100 psi) are significantly lower than composite pipe. Similar to composite pipe, there are no standards for the transport of hydrogen and carbon dioxide, though HDPE pipe’s lower pressure limits make it less suited for use in carbon capture and storage.
With strategic investment, cross-sector coordination, and long-term planning, it is possible to reduce risks and protect vulnerable communities. We can build a future where power lines no longer spark disaster and homes stay safe and connected — no matter the weather.
Confronting this crisis requires decision-makers to understand the lived realities of wildfire risk and resilience, and to work together across party lines. Safewoods helps make both possible.
Yesterday, the U.S. Environmental Protection Agency proposed revoking its 2009 “endangerment finding” that greenhouse gases pose a substantial threat to the public. The Federation of American Scientists stands in strong opposition.
The Federation of American Scientists supports H.R. 4420, the Cool Corridors Act of 2025, which would reauthorize the Healthy Streets program through 2030 and seeks to increase green and other shade infrastructure in high-heat areas.